Applied Thermodynamics
Unit 1: Fuels and Combustion
1. Types of Fuels
Fuels can be broadly categorized into two types: conventional fuels and renewable fuels.
1.1 Conventional Fuels
These are the most commonly used fuels and include:
- Fossil Fuels: Such as coal, oil, and natural gas. They are derived from the remains of ancient organisms and are primarily hydrocarbons.
- Biofuels: Derived from organic materials, including biomass, biodiesel, and ethanol.
- Nuclear Fuels: Such as uranium and thorium, used in nuclear reactors.
1.2 Renewable Fuels
These fuels are generated from renewable resources and include:
- Solar Energy: Captured through solar panels to produce electricity or heat.
- Wind Energy: Harnessed through wind turbines.
- Hydropower: Generated from the flow of water.
2. Calorific Values of Fuel and Its Determination
The calorific value (CV) of a fuel is the amount of energy released when a unit quantity of fuel is completely burned. It is expressed in units such as MJ/kg or kcal/kg. There are two types of calorific values:
2.1 Higher Calorific Value (HCV)
This value includes the total energy released, including the energy from the condensation of water vapor in the combustion gases.
2.2 Lower Calorific Value (LCV)
This value excludes the energy from the condensation of water vapor, as it is not recoverable in practical applications.
2.3 Determination of Calorific Value
The calorific value can be determined using a bomb calorimeter. The process involves:
- Weighing a sample of fuel and placing it in the calorimeter.
- Igniting the sample and measuring the temperature change in the surrounding water.
- Calculating the energy released using the specific heat capacity of water.
Figure 1: Bomb Calorimeter Setup
3. Combustion Equations for Hydrocarbon Fuels
Combustion is a chemical reaction between a fuel and an oxidizer, producing heat and light. For hydrocarbon fuels, the general combustion equation can be represented as:
Where a, b, and c are stoichiometric coefficients determined by balancing the equation.
3.1 Example of Combustion of Methane (CH4)
The balanced combustion equation for methane is:
This equation shows that one mole of methane reacts with two moles of oxygen to produce one mole of carbon dioxide and two moles of water.
4. Determination of Minimum Air Required for Combustion and Excess Air Supplied
The amount of air required for combustion depends on the fuel type and composition. For complete combustion, a stoichiometric amount of air is needed.
4.1 Minimum Air Required
The minimum air required for complete combustion can be calculated using:
Where:
- A = Air required (in m3)
- a = Moles of oxygen needed
4.2 Excess Air Supplied
Excess air is the air supplied beyond the stoichiometric requirement, which helps to ensure complete combustion. It is usually expressed as a percentage:
This ensures that there is sufficient oxygen to completely react with the fuel.
5. Conversion of Volumetric Analysis to Mass Analysis
Volumetric analysis is commonly used to express concentrations of gases, but mass analysis can provide a clearer understanding of energy content. The conversion can be done using the following relationship:
This formula allows us to convert the percentage composition of gases from volumetric to mass terms, which is useful in combustion calculations.
6. Fuel Gas Analysis
Fuel gas analysis involves determining the composition of fuel gases, which is critical for combustion efficiency and emission control. The analysis typically includes measuring the concentrations of:
- Methane (CH4): The primary component of natural gas.
- Carbon Dioxide (CO2): A product of combustion.
- Carbon Monoxide (CO): A toxic gas that can result from incomplete combustion.
- Hydrogen Sulfide (H2S): A harmful gas often found in natural gas.
6.1 Methods of Gas Analysis
Common methods for analyzing fuel gases include:
- Gas Chromatography: Separates and analyzes compounds in gases.
- Infrared Spectroscopy: Measures the absorption of infrared light by gas molecules.
Unit 2: Steam Generators
1. Classification of Boilers
Boilers can be classified based on various criteria, such as:
1.1 Based on the Water-Tube Design
- Fire Tube Boilers: Hot gases pass through tubes surrounded by water. They are simpler, less expensive, and suitable for lower pressures.
- Water Tube Boilers: Water circulates through tubes heated by hot gases. They can withstand higher pressures and are used for larger capacities.
1.2 Based on the Boiler Working Pressure
- Low-Pressure Boilers: Operate at pressure below 1 MPa (10 bar).
- High-Pressure Boilers: Operate above 1 MPa (10 bar).
1.3 Based on the Fuel Used
- Solid Fuel Boilers: Use coal, wood, etc.
- Liquid Fuel Boilers: Use oil or diesel.
- Gas Fuel Boilers: Use natural gas, LPG, etc.
2. Requirements of a Good Boiler
A good boiler must meet the following criteria:
- Safety: Must operate under safe pressure and temperature limits.
- Efficiency: High thermal efficiency to minimize fuel consumption.
- Durability: Made from quality materials to withstand pressure and temperature.
- Ease of Maintenance: Design should allow for easy cleaning and repairs.
- Compactness: Should occupy minimal space for installation.
3. Merits and Demerits of Fire Tube and Water Tube Boilers
3.1 Fire Tube Boilers
Merits:
- Lower initial cost and simpler design.
- Easy to operate and maintain.
Demerits:
- Limited to lower pressures (up to 2.5 MPa).
- Longer steam-raising time.
3.2 Water Tube Boilers
Merits:
- Suitable for high pressures (up to 10 MPa or more).
- Quick steam generation and higher efficiency.
Demerits:
- Higher initial cost and complex design.
- Requires skilled operation and maintenance.
4. Boiler Mountings and Accessories
Boiler mountings are essential fittings required for the safe operation of the boiler, including:
- Safety Valve: Prevents excessive pressure buildup.
- Water Level Indicator: Shows the water level in the boiler.
- Pressure Gauge: Measures steam pressure within the boiler.
- Blowdown Valve: Removes sediment and impurities from the boiler water.
Accessories enhance the efficiency and performance of the boiler, such as:
- Feed Pump: Supplies water to the boiler.
- Economizer: Recovers waste heat to improve efficiency.
- Superheater: Increases steam temperature beyond saturation.
5. Boiler Draught
Draught refers to the pressure difference that causes the flow of air into the furnace for combustion. It can be classified as:
5.1 Natural Draught
Generated by the difference in density between hot gases inside the boiler and cooler outside air. It requires no mechanical assistance.
5.2 Mechanical Draught
Created using fans or blowers to force or pull air into the furnace, enhancing combustion efficiency.
5.3 Efficiency of the Chimney
The efficiency of a chimney is determined by its height and the temperature difference between the flue gases and ambient air. The chimney should be designed to minimize draught losses.
5.4 Draught Losses
Draught losses can occur due to:
- Friction in the flue gas path.
- Obstruction in the chimney.
6. Performance of Boilers
6.1 Evaporation
Evaporation refers to the process of converting water into steam. It is a critical measure of a boiler’s performance.
6.2 Equipment Evaporation
Equipment evaporation is defined as the amount of steam generated per unit of fuel consumed, typically expressed in kg of steam per kg of fuel.
6.3 Boiler Efficiency
Boiler efficiency is defined as the ratio of useful energy output to the energy input, expressed as:
Where:
- η = Efficiency (%)
- Q = Quantity of steam produced (kg)
- H = Enthalpy of steam (kJ/kg)
- F = Quantity of fuel used (kg)
- CV = Calorific value of fuel (kJ/kg)
6.4 Boiler Trial and Heat Balance
A boiler trial involves measuring the performance parameters of the boiler under actual operating conditions to determine its efficiency and effectiveness. Heat balance calculations help identify energy losses.
6.5 Introduction to IBR
The Indian Boiler Regulations (IBR) govern the design, construction, and operation of boilers in India. They ensure safety and efficiency standards are met in boiler operations.
Unit 3: Vapor and Gas Power Cycles, Steam Nozzles
1. Ideal Rankine Cycle
The Ideal Rankine Cycle is a thermodynamic cycle that converts heat into work using water as the working fluid. It consists of four processes:
- Isentropic Compression: Water is pumped from the condenser pressure to boiler pressure.
- Isobaric Heat Addition: Water is heated at constant pressure to become steam.
- Isentropic Expansion: Steam expands through a turbine, doing work.
- Isobaric Heat Rejection: Steam is condensed back into water at constant pressure.
Thermal Efficiency
The thermal efficiency of the Rankine cycle can be calculated using:
Where Wnet is the net work output, Qin is the heat input, and h values are the specific enthalpies at different states.
2. Reheat and Regeneration
2.1 Reheat Cycle
In the reheat cycle, steam is partially expanded in the turbine, returned to the boiler for reheating, and then expanded again. This improves efficiency by allowing the steam to do work at higher temperatures.
2.2 Regeneration
Regeneration involves using steam extracted from the turbine to preheat the feedwater, thus reducing the heat input required in the boiler.
3. Stirling Cycle
The Stirling cycle is a closed regenerative cycle consisting of two isothermal processes and two isochoric processes. It uses a constant amount of working fluid and is known for high efficiency and low emissions.
- Isothermal Expansion: The gas expands at a constant high temperature, doing work on the piston.
- Isochoric Cooling: The gas is cooled at constant volume, reducing pressure.
- Isothermal Compression: The gas is compressed at a constant low temperature, requiring work input.
- Isochoric Heating: The gas is heated at constant volume, increasing pressure.
4. Joule-Brayton Cycle
The Joule-Brayton cycle (or Brayton cycle) is the ideal cycle for gas turbines, consisting of two adiabatic processes and two isobaric processes. The main components are the compressor and the turbine.
- Adiabatic Compression: Air is compressed, raising its pressure and temperature.
- Isobaric Heat Addition: Fuel is injected and combusted, increasing energy.
- Adiabatic Expansion: The high-pressure gas expands through the turbine, generating work.
- Isobaric Heat Rejection: The exhaust gases are released at lower pressure.
Thermal Efficiency
The thermal efficiency of the Joule-Brayton cycle can be calculated as:
Where T1 and T2 are the inlet and outlet temperatures, and k is the specific heat ratio (Cp/Cv).
5. Calculation of Specific Steam/Fuel Consumption
Specific steam consumption (SSC) is the amount of steam produced per unit of fuel consumed, given by:
Where mfuel is the mass of fuel used, and msteam is the mass of steam produced.
6. Steam Nozzles
Steam nozzles are devices that convert thermal energy in steam to kinetic energy, allowing for efficient expansion and flow control. They are characterized by:
6.1 Types of Nozzles
- Converging Nozzles: Increase velocity as steam flows through a narrowing passage.
- Diverging Nozzles: Used to accelerate steam at supersonic speeds.
6.2 Flow of Steam through Nozzles
As steam passes through the nozzle, its pressure decreases while its velocity increases, resulting in kinetic energy conversion.
6.3 Condition for Maximum Discharge
Maximum discharge through a nozzle occurs when:
Where A is the area, P1 is the upstream pressure, and P2 is the downstream pressure.
6.4 Expansion of Steam Considering Friction
Friction reduces the velocity and pressure drop in steam nozzles, requiring modifications in calculations to account for these losses.
6.5 Super Saturated Flow through Nozzles
Super saturation occurs when steam enters a nozzle as wet steam and exits as a dry saturated or superheated steam, affecting efficiency and performance.
6.6 General Relationship between Area, Velocity, and Pressure
The flow through nozzles can be expressed as:
Where A is the area and V is the velocity of steam.
Unit 4: Condensers, Cooling Towers, and Steam Turbines
1. Condensers and Cooling Towers
1.1 Elements of Steam Condensing Plants
A steam condensing plant typically consists of the following elements:
- Condenser: Cools steam back into liquid water.
- Cooling Water System: Provides cooling water for heat exchange.
- Pumps: Circulate condensate and cooling water.
- Heat Exchangers: Enhance heat transfer between steam and cooling water.
1.2 Advantages of Using Condensers
Condensers improve the efficiency of steam plants by:
- Reducing back pressure on the turbine.
- Recycling condensate for boiler feedwater.
- Increasing thermal efficiency of the cycle.
1.3 Types of Condensers
- Surface Condenser: Uses a heat exchanger to condense steam.
- Jet Condenser: Mixes steam with cooling water directly.
- Barometric Condenser: Relies on atmospheric pressure to assist in condensation.
1.4 Thermodynamic Analysis of Condensers
The condenser operates under the principle of heat transfer, where steam loses heat to the cooling water:
Where Qout is the heat rejected, msteam is the mass flow rate of steam, and h values are specific enthalpies.
1.5 Efficiencies of Condensers
Efficiency is typically measured as the ratio of actual cooling to theoretical cooling:
1.6 Cooling Towers
Cooling towers dissipate heat from cooling water used in condensers to the atmosphere. They operate on the principle of evaporative cooling.
- Natural Draft Towers: Rely on buoyancy to create airflow.
- Mechanical Draft Towers: Use fans to force air through the tower.
2. Steam Turbines
2.1 Advantages of Steam Turbines
Steam turbines are widely used due to their:
- High efficiency and power output.
- Ability to operate with various steam conditions.
- Compact design compared to reciprocating engines.
2.2 Classification of Steam Turbines
Steam turbines can be classified based on:
- Impulse Turbines: Steam expands in nozzles before striking turbine blades.
- Reaction Turbines: Steam expands while passing through the blades, causing rotation.
2.3 Compounding of Steam Turbines
Compounding allows steam to expand in stages, reducing the velocity of steam and improving efficiency. Common methods include:
- Pressure Compounding: Using multiple pressure stages.
- Velocity Compounding: Utilizing multiple sets of blades for a single pressure stage.
2.4 Velocity Diagrams
Velocity diagrams illustrate the relationships between the inlet and outlet velocities of steam in the turbine. They help in determining:
- Blade angles.
- Work done per stage.
2.5 Work Done and Efficiencies
The work done by a steam turbine is given by:
Where Wturbine is the work output and h values are specific enthalpies.
2.6 Losses in Turbines
Common losses in steam turbines include:
- Mechanical Losses: Friction and windage losses.
- Thermodynamic Losses: Inefficiencies in steam expansion.
- Leakage Losses: Steam escaping from seals.
Unit 5: Reciprocating Air Compressor
1. Reciprocating Air Compressor
1.1 Classification
Reciprocating air compressors can be classified based on:
- Single-acting Compressors: Air is compressed on one side of the piston.
- Double-acting Compressors: Air is compressed on both sides of the piston.
- Positive Displacement Compressors: Compress air by reducing its volume.
- Dynamic Compressors: Compress air by imparting velocity to the air.
1.2 Constructional Details
A typical reciprocating air compressor consists of the following components:
- Piston: Moves within the cylinder to compress air.
- Cylinder: Encloses the piston and provides a chamber for compression.
- Crankshaft: Converts rotary motion into linear motion for the piston.
- Valves: Control the intake and exhaust of air.
1.3 Theoretical and Actual Indicator Diagram
The indicator diagram represents the pressure-volume (P-V) relationship during the compression cycle:
Theoretical diagrams assume ideal conditions, while actual diagrams account for real-world inefficiencies.
1.4 Free Air Delivery (FAD)
FAD is defined as the volume of air delivered by the compressor corrected to standard conditions:
Where Vactual is the actual volume delivered, Pabs is the absolute pressure, and Pstd is the standard pressure.
1.5 Multi-Staging
Multi-staging involves using two or more cylinders to compress air in stages, which improves efficiency and reduces the temperature of the compressed air. The process includes:
- Intercooling between stages to remove heat.
- Higher overall efficiency compared to single-stage compression.
1.6 Conditions for Maximum Efficiency
Maximum efficiency in reciprocating compressors is achieved under the following conditions:
- Proper valve timing to minimize losses.
- Optimal piston speed to avoid excessive friction and heat.
- Correct choice of cylinder diameter and stroke length.
1.7 Capacity Control
Capacity control methods are used to adjust the output of the compressor according to demand. Common methods include:
- Variable Speed Drives: Adjusting the speed of the motor driving the compressor.
- Unloaders: Allowing air to bypass the cylinder when not in use.
- Multi-stage Operation: Using multiple stages to handle varying loads efficiently.
2. Rotary Compressors
2.1 Concepts of Rotary Compressors
Rotary compressors use a rotating mechanism to compress air. They are known for their smooth operation and continuous flow.
2.2 Types of Rotary Compressors
- Root Blower: A positive displacement compressor that uses two rotors to compress air.
- Centrifugal Compressors: Utilize a rotating impeller to increase the velocity of air, converting kinetic energy into pressure energy.
2.3 Velocity Diagram
The velocity diagram for a centrifugal compressor illustrates the relationship between the inlet and outlet velocities of the air.
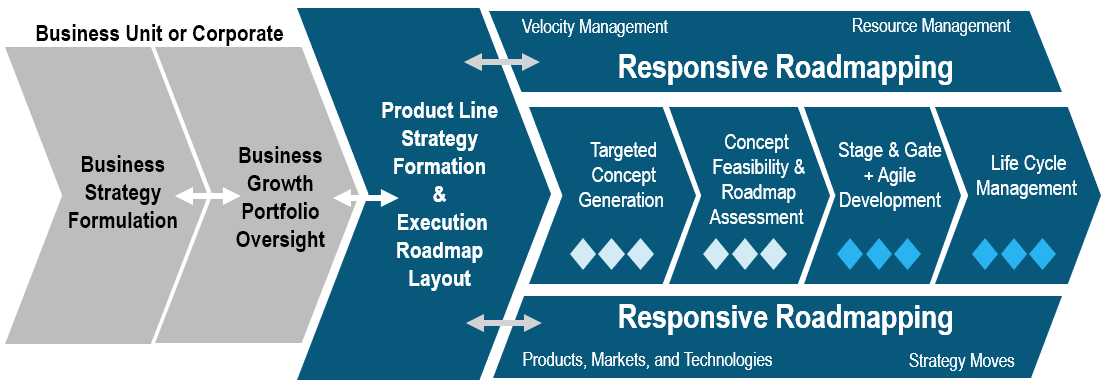
2.4 Construction and Expression for Work Done
The construction of a rotary compressor includes the rotor, casing, and drive mechanism. The work done by a centrifugal compressor is expressed as:
Where P represents pressures and V is the volume flow rate.
2.5 Introduction to Slip Factor
The slip factor accounts for the difference between the theoretical and actual performance of a compressor. It is defined as:
2.6 Power Input Factor
The power input factor indicates the efficiency of the compressor in converting input power to useful work. It is expressed as:
Texts:
1. T. D. Eastop, A. McConkey, “Applied Thermodynamics”, Addison Wesley Longman.
2. Rayner Joel, “Basic engineering Thermodynamics”, Addison Wesley Longman.
References:
1. Yunus A. Cengel, “Thermodynamics- An Engineering Approach”, Tata McGraw Hill
Publications.
2. P. K. Nag, “Basic and Applied Thermodynamics”, Tata McGraw Hill Publications.
3. P. K. Nag, “Power Plant Engineering”, Tata McGraw Hill Publications, 2
nd edition.
4. Sharma and Mathur, “Internal Combustion Engines”, Tata McGraw Hill Publications.